General considerations:
Pilot plant scale-up is an intermediate step between the lab and full-scale commercial production, allowing industries to test and refine processes, gather data, and evaluate production feasibility.
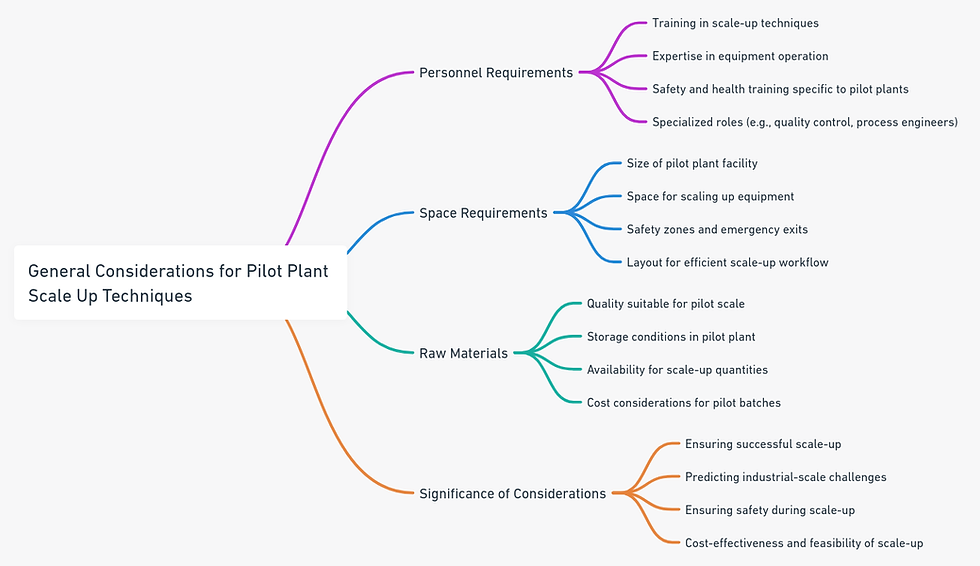
Here are some general considerations:
1. Personnel Requirements:
a. Expertise and Training:
With the scaling up from a laboratory to a pilot plant, the complexity of operations also increases.
Hence, personnel with the right expertise and training in the scale-up process, equipment handling, and safety protocols become essential.
b. Cross-functional Collaboration:
pilot plant often involves the collaboration of multiple departments such as R&D, engineering, quality control, and production.
Effective communication and teamwork among these departments are crucial.
c. Safety:
Safety training becomes more critical at the pilot scale because larger volumes and flow rates can pose increased risks.
All personnel should be trained in emergency response and standard operating procedures (SOPs).
2. Space Requirements:
a. Equipment size:
Pilot scale equipment is larger than lab scale but smaller than industrial scale, which means that the space required will be significantly more than a lab but less than a full-scale plant.
b. Safety considerations:
Adequate spacing between equipment is essential to prevent accidents, allow for maintenance work, and accommodate safety equipment such as fire extinguishers and showers.
c. Storage:
Adequate space is required for storing raw materials, intermediates, final products, and waste.
Additionally, provisions should be made for sample collection and testing areas.
d. Flexibility:
As the pilot plant is often used to test and refine processes, space considerations should account for potential reconfigurations of equipment and process lines.
3. Raw Materials:
a. Quantities:
More raw material is required compared to the lab scale but significantly less than commercial scale.
The procurement process may change, and bulk purchasing might be introduced.
b. Quality:
The quality of raw materials used in pilot plants should ideally be the same as that intended for commercial production to ensure consistency in results and to identify any potential challenges early.
c. Storage:
With increased raw material quantities, considerations around storage conditions, shelf life, and inventory management become crucial.
d. Waste management:
Larger quantities of raw materials also lead to increased generation of waste.
Proper disposal methods and waste treatment should be considered.
Significance:
Properly trained and skilled personnel are the backbone of a successful pilot plant operation. They ensure the production processes are carried out effectively, safely, and in compliance with regulations.
Adequate space is crucial for the smooth and safe operation of a pilot plant. It ensures that equipment can be operated effectively and safely, and that personnel can work efficiently without unnecessary risks.
High-quality raw materials are the foundation of pharmaceutical production. Without consistent, high-quality raw materials, it is impossible to produce a consistent, high-quality final product. Proper storage and documentation of these materials are also critical for both quality control and regulatory compliance.
These considerations are fundamental in setting up and operating a pilot plant effectively, ensuring product quality, worker safety, and regulatory compliance, and ultimately facilitating a successful scale-up to commercial production.